CHINAPLAS 2023 | Let's Make Pipe Production More Simple More Accuracy
We will show a complete extrusion mixing and dosing system combined with independently developed flexible control systems at Chinaplas 2023, to achieve simplified material mixing before extrusion, online mixing and dosing, precise measurement and stable feeding.
The new generation of flexible control systems will add three new modules: predictive maintenance, remote penetration, and energy analysis, which will make pipe production more simple, more accuracy!
Show the highlights of LIANSU!
· 20~1200mm HDPE multi-layer pipe co-extrusion technology ·
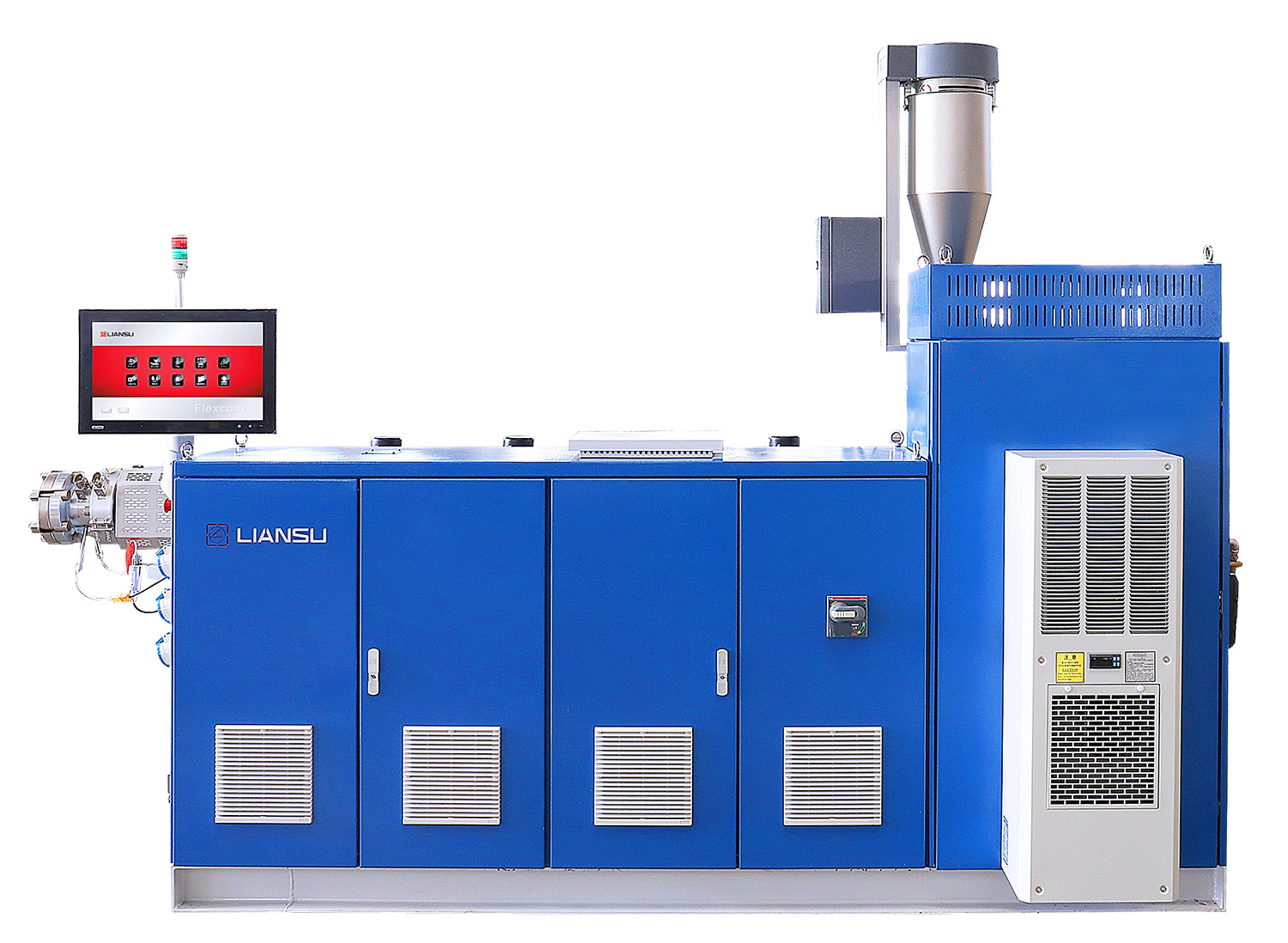
To ensure high efficiency, low consumption, and low melt temperature, this extrusion equipment adopts a 40 L/D ratio screw and spiral sleeve, matched with a dedicated permanent magnetic servo motor. The extrusion fore-end adopts integrated precision weight control to flexibly adjusted the material ratio online. Due to the Flexcon+flexible control system, it can provide equipment data collection and processing, and add predictive maintenance to the gear box on the basis of existing maintenance. Material measurement, vacuum control, and finished product weight are all controlled by closed-loop control.
Configure a melt cooler for the extrusion of large-diameter pipes to stabilize the melt temperature before the material enters the mould and prevent sagging.
The multi-layer pipe mould adopts a spiral basket structure and a multi spiral flow channel distribution body design. Through CAE finite element simulation analysis, it ensures the uniformity of the thickness of each layer of the pipe. Reasonable flow channel volume and smaller mould volume reduce melt residence time, faster color change time, and the mould can quickly heat up, requiring less insulation energy consumption. Equipped with internal cooling function for efficient cooling, the same cooling length can achieve higher production. The mould design adapts to a wide range of specifications, which can reduce investment and change specifications faster. The mould has low back pressure, extremely low energy consumption and simple maintenance.
· PVC Parallel Twin-screw Extruder + Online Mixing and Dosing System ·
It has a 36D L/D ratio screw for the parallel twin-screw extruder, the main motor adopts IE4+dedicated permanent magnet servo motor, combined with an online PVC mixing and dosing system and 4 sets of online loss-in-weight feeder, to achieve online continuous dosing and mixing of PVC, calcium carbonate, ONEPACK formula materials, and color powder materials for precise quantitative feeding.
Equipped with a self-developed Flexcon+ flexible control system and an energy analysis module for the entire production process, it can achieve real-time energy consumption monitoring and analysis of each pipe, including energy analysis throughout the entire production process from the feeding system to extrusion and online packaging. It can also achieve real-time monitoring of production data, data collection, data processing, optional predictive maintenance system for screws and gear boxes, and closed-loop control function for extrusion equipment.
More new products and configurations will be displayed at our stand. Stay tuned!
April 17th-20th, 2023
Shenzhen · China
Hall8 · H41